What are key figures needed for in production and quality assurance?
Production processes are complex. Plant availability, production output, production costs and production quality are influenced by many adjacent functions that interact with each other and with production. Accordingly, the assessment of production performance must be multi-faceted. A single performance figure can provide an overall view, but it is not suitable for specifically capturing the actual conditions in production and optimizing them. Other key performance indicators are required for operational management and improvement of key production data.
It makes sense not only to use simple measured values in production, but also key figures that relate different measured values to each other or measured values to targets. In this way, dependencies can be shown.
In addition, time series of key figures are recommended in order to recognize tendencies and to guide developments.
Which key figures are useful for production and quality assurance?
There are key figures for overall plant effectiveness, for plant availability, for production output, for the achieved quality of the products, for employee effectiveness and for production costs.
Plant effectiveness: How can plant effectiveness be positively influenced?
Production effectiveness is measured in terms of machine or plant availability, production output and the quality of the production results achieved. This production effectiveness is reflected by the fundamental key figure of Overall Equipment Effectiveness (OEE). The Overall Equipment Effectiveness OEE is calculated as the product of the equipment availability A, the production performance P and the quality achieved Q.
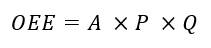
Production output: How can production output be increased?
The production quantity is the number of pieces or, in the process industry, the quantity of goods produced, including the quantity to be reworked and the scrap.
Production volume is relevant to costs, but also determines sales opportunities. A growth strategy also requires an increase in production volume. The actual production volume depends on the theoretical capacity, plant availability and plant performance.
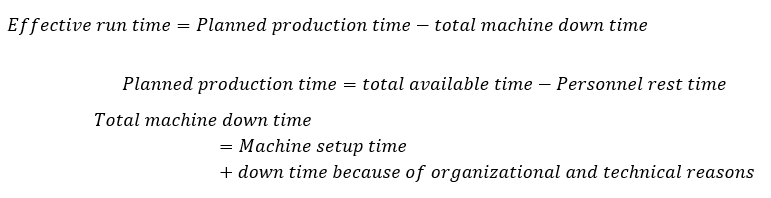
Production costs: How can production costs be measured?
Production cost is the total of all costs incurred to produce goods. Included in production costs are the costs of raw materials or input materials, purchased components and auxiliary materials, the costs of direct and indirect personnel and workplaces used in production, the costs of machinery and equipment, tooling costs, energy costs, maintenance and repair costs and the costs of buildings used for production purposes, warehousing costs and costs of business insurance.
Of interest are the direct personnel costs incurred for a given production quantity. This key figure can be influenced by the working methods of the direct personnel in production.

Production costs: How can production costs be measured?
Production cost is the total of all costs incurred to produce goods. Included in production costs are the costs of raw materials or input materials, purchased components and auxiliary materials, the costs of direct and indirect personnel and workplaces used in production, the costs of machinery and equipment, tooling costs, energy costs, maintenance and repair costs and the costs of buildings used for production purposes, warehousing costs and costs of business insurance.
Of interest are the direct personnel costs incurred for a given production quantity. This key figure can be influenced by the working methods of the direct personnel in production.
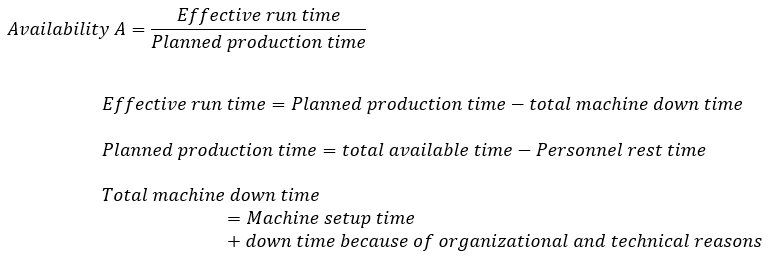
The formulas show the levers for effective measures with which production availability can be optimized.
Setup times are capacity and material killers and should therefore be minimized. Setup times can be minimized by production lot sizes and by linking similar production orders for which only minor adjustments need to be made to the machine and tool settings. This is referred to as production linking. In addition, setup times can be reduced by standardizing parts and components.
Among other things, availability is influenced by the reliability of machinery and equipment. A common key figure for reliability is the Mean Time to Repair (MTTR).

Another key figure useful for production is the Mean Time between Failure (MTBF), which shows the reliability of machines and systems. MTBF indicates the average time during which the machine or system operates without malfunction. It is thus a measure of the process risk.

Production failures: How can production downtime be measured in a meaningful way?
Production downtimes can be listed. Modern CNC machines linked to a production data acquisition system can automatically record production downtimes with their times. Reasons can be assigned to the downtimes. On a rough level, a distinction is made between organizational and technical reasons. Organizational reasons include, for example, lack of materials, lack of personnel and additional setup operations required at short notice. Technical reasons include plant faults, unsuitable starting material, tool breakage and recognized quality defects.

Derived from the MTBF, the Probability Failure per Hour (PFH) is also used as a key figure that reflects the average probability of a failure per hour.
In mechanical and plant engineering, where smaller batch sizes are produced, the “Performance Level” is often used in accordance with EN ISO 13849-1. In the process industry and in manufacturing companies with large batch sizes (mass production), the “Safety Integrity Level” according to IEC 62061 is popularly used, which was originally developed for electrical, electronic systems and for programmable systems.
Production scrap: How can production scrap be monitored and assessed?
Production scrap is another important production metric. Production scrap is measured as the quotient of the scrap quantity divided by the total production quantity.

Particularly in the case of the scrap ratio, attention must be paid to what the scrap refers to: to the total production quantity or to the yield. For low scrap rates, this distinction is irrelevant. However, if 50% of the quantity produced is scrap, then the scrap in relation to the yield is 100%. This extreme example illustrates how misunderstandings can arise if the reference quantity is not clearly defined.
Scrap consumes material, causes personnel costs and passes through production machines, thus taking up capacity and energy.
Delivery reliability: How many orders are delivered completely and on time?
Delivery reliability is significantly, but not exclusively, influenced by production. It is defined by the proportion of orders that are delivered in full and on time as a percentage of the total number of orders. Delivery reliability is defined by the supply chain management metric OTIF (on-time in full).
To determine OTIF, the number of orders that have been shipped out or delivered on the agreed date (OT) and the number of orders that have been delivered in full (IF) must be recorded.

Maintenance costs: How can maintenance costs be monitored?
Maintenance and repair costs increase with increasing machine age. At the same time, financing costs decrease when machines are largely paid off. In this respect, maintenance and repair costs compete with investments for new machines or equipment.
Arguments against old machines can be the decreasing reliability and availability. As the risk of failure increases, process quality decreases throughout production and throughout the company. Resulting production backlogs can cause very high costs. For machines that are only used occasionally, this consideration may not be critical, but for machines that have a significant influence on the production process, an analysis is recommended as a basis for decision-making.
In this respect, it is advisable to weigh the total costs for existing machines against the total costs for new machines.
Investment costs: How can investments be assessed?
New machines or systems incur acquisition, installation and start-up costs that have to be financed, but they often work significantly faster than old existing machines; this allows capacity and efficiency advantages to be tapped. As a rule, they also operate more energy-efficiently than old equipment. In addition, new machines typically work more precisely, so that higher customer requirements for precision can be met.
With a careful investment calculation, the relative advantages of an investment can be worked out.